Summary
We are excited to announce our investment in Xefco, a Geelong-based start-up that has developed a novel technology for dyeing and finishing textiles. It uses 99% less water, 90% less energy and 97% less chemicals than the conventional process. This is Virescent’s 34th investment on behalf of the Clean Energy Finance Corporation.
The investment is part of Xefco’s $10.5m seed extension round, alongside Main Sequence Ventures, Breakthrough Victoria and Investible.
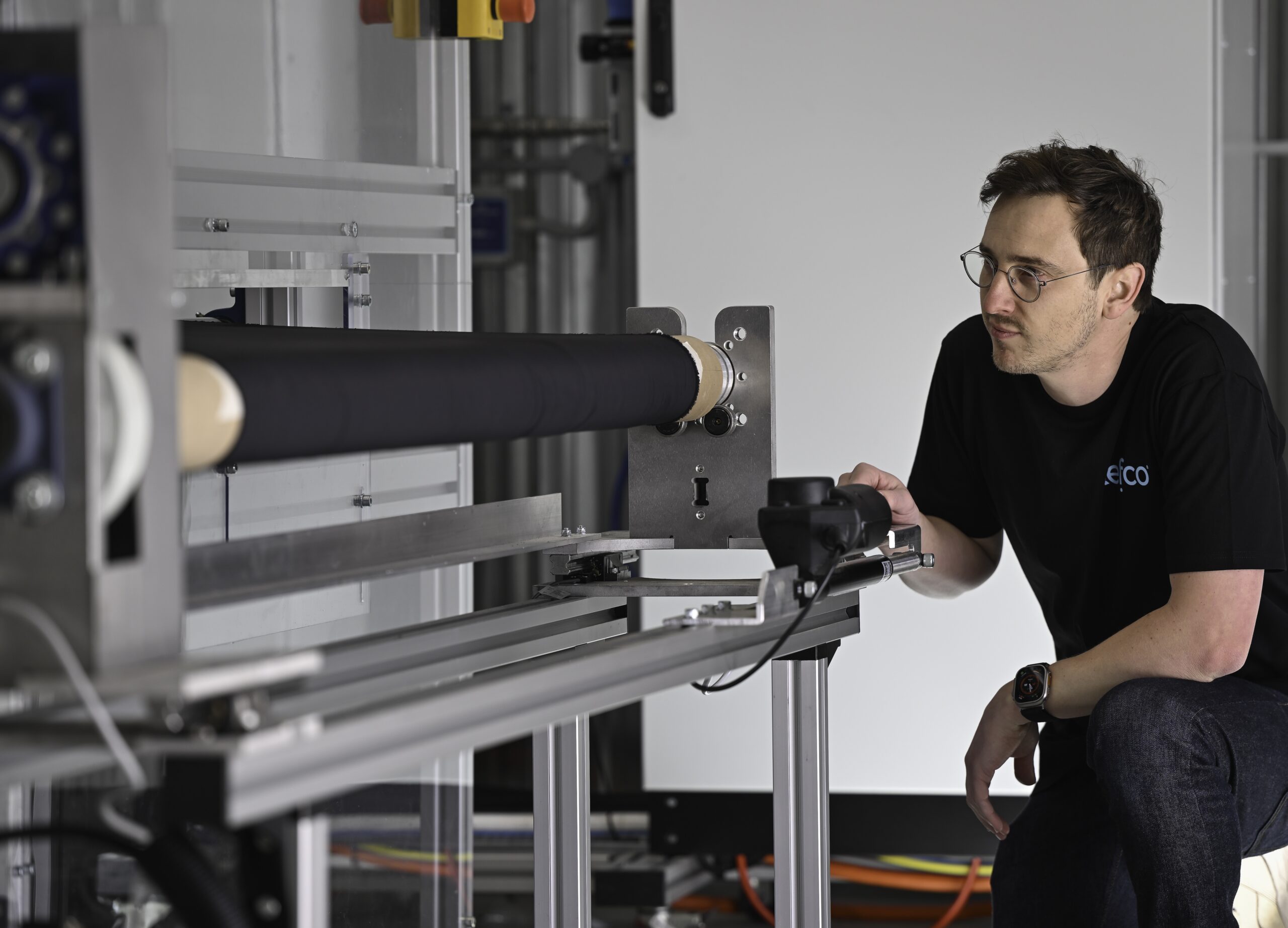
Xefco Founder Tom Hussey
What’s wrong with textile dyeing today?
The textile industry is one of the world’s biggest polluters – greenhouse gas emissions from the sector are greater than international aviation and shipping combined.[1]

Breakdown of textile industry CO2e emissions, by manufacturing stage[2]
The dyeing and finishing stage of textile manufacturing involves taking undyed, woven fabric and applying both colours and finishing effects (such as water repellency, flame retardancy, crease and antibacterial resistance). It is the last stage before the fabric is sent to garment assemblers for cutting and sewing. As shown above, this stage is the most carbon intensive step in the manufacture of clothing. It accounts for 1%[3]-3%[4] of global carbon emissions, 20%[5] of global industrial water pollution and 25%[6] of chemicals produced globally.
Fabrics are conventionally wet-dyed (soaked in vessels full of dye and chemicals heated up to 100°C – typically using coal and gas-fired boilers), dried (to remove excess moisture) and finished (to bond the colour to the textile and apply treatments such as waterproofing) in three distinct batch steps. The conventional process requires up to 11 separate machines and is highly capital intensive.
Despite some green shoots, the core technology has remained largely unchanged for decades and has been slow to decarbonise. As one dyeing expert put it to us: “I walk into dye houses today and the technology is the same as what I was using as an operator 28 years ago”.
Enter Xefco
Xefco’s Ausora machine is a continuous process that sprays coloured pigment onto the textile and then uses atmospheric pressure plasma-enhanced chemical vapour deposition (“PECVD”) technology to bond the colour and apply further finishing treatments. PECVD under vacuum pressureis commonly used to produce thin-film coatings in the manufacture of semi-conductors, touch panel displays and other advanced electronics. However, vacuum PECVD is slow due to the requirement to pump air from the chamber for each batch; this works in the high-margin semiconductor and electronics manufacturing industries, but not in the high-volume and low-margin textiles game.

Xefco’s CEO Tom Hussey explains the technology to Virescent Ventures’ Chair, John Clifford
The Founders’ story
Xefco’s co-founders Tom Hussey and Brian Conolly met through previous company Zhik, a sailing apparel start-up founded by Brian and where Tom was Head of R&D. At Zhik they began experimenting with high performance, environmentally-friendly textile coatings. After realising the potential of the Ausora technology when applied to standard clothing (instead of wetsuits and yachting apparel) they acquired the IP from Zhik to bring it to a broader audience. Xefco was established in 2018 and is based at Deakin University’s ManuFutures hub at the Waurn Ponds campus.
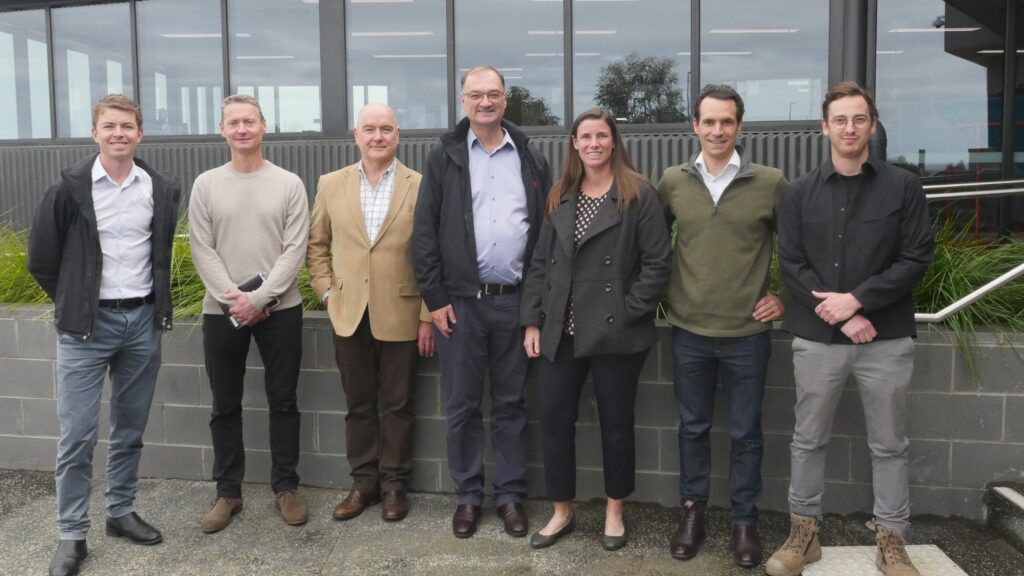
The Virescent Ventures team with Xefco’s CEO Tom Hussey
Why we invested
- A huge global market with a burning platform to improve environmental credentials: Companies playing in theUS$300b p.a. textile dyeing and finishing market have never faced more scrutiny over their environmental footprint. In the EU, brands will be required to report Scope 3 emissions from 2025 and introduce traceable Digital Product Passports that show product impact from 2030. Unlike previous eras, companies are now walking the talk – hundreds of global brands have publicly committed to aggressive 2030 emissions reduction targets.
- A defensible technology, with potential to compete on unit economics: The fashion industry is notoriously cost sensitive. What’s exciting is we think that Xefco’s environmental benefits translate into potentially large savings in energy and chemical costs – giving Xefco a pathway to compete on both opex and capex with conventional processes. One of Xefco’s first hires was a patent attorney, and they have a carefully constructed patent portfolio that covers the process, the end-product, and some supporting technologies.
- A deep pipeline of interest from brands and mills: Xefco are pursuing a ‘push-pull’ go-to-market strategy where they are demonstrating the technical advantages of Ausora to mill customers (the push), while selling the environmental benefits to their brand customers (creating pull-through). Xefco is collaborating with 10 major apparel brands (total revenue over US$100b) and 7 major mills (total production over 1b metres per year). We expect early adopters to include mills facing water scarcity issues or decarbonisation pressures from brands.
- A team with deep textiles knowledge and access to leading university support: Tom andBrian both have about 15 years commercialising innovations in the textile industry. We’ve been impressed with the resourcefulness of the team – with just $6m raised, Xefco are now onto their third-generation system, capable of processing 1 metre per minute. For context, that’s a 5x scale-up away from a commercial system. The founders are surrounded by a team of highly credentialled plasma physicists and industrial engineers. To date, Xefco has been awarded over $6 million in grant funding through the likes of Deakin University’s Recycling and Clean Energy Commercialisation Hub (REACH), Future Fibres Hub, and Innovative Manufacturing CRC (IMCRC).
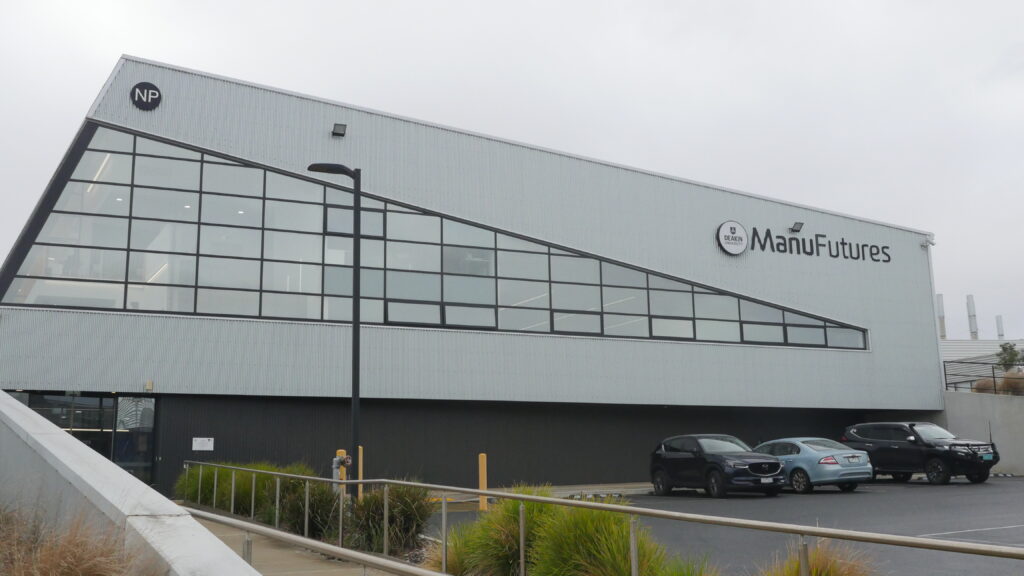
Deakin University’s ManuFutures facility – home to Xefco’s research and hardware manufacturing
We look forward to supporting the Xefco team to help transform the clothing industry.
Got questions or interested in learning more about Xefco? Contact Alex Oppes
[1] McKinsey & Company, What is fast fashion?, December 7, 2023.
[2] Quantis, “Measuring Fashion Environmental Impact of Global Apparel and Footwear Industries Study” (2018)
[3] World Resources Institute and the Apparel Impact Institute, “Roadmap to Net Zero: Delivering Science-Based Targets in the Apparel Sector” (2021) estimates apparel is responsible for 2% of global emissions x dyeing and finishing’s 52% contribution.
[4] Quantis, “Measuring Fashion Environmental Impact of Global Apparel and Footwear Industries Study” (2018) estimates apparel and footwear industries are responsible for 8.1% of global emissions x dyeing and finishing’s 36% contribution.
[5] Kant, R. “Textile Dyeing Industry: An Environmental Hazard”. Natural Science 4 1, 22–26 (2012).
[6] Choi, J. et. al. “Dirty Laundry: Unravelling the Corporate Connections to Toxic Water Pollution in China, Amsterdam” (2011).